The Warehouse Management Software for increased productivity
Warehouse management software helps you take control of your tasks and increase staff productivity. Saving you time and money through intuitive automation.
Warehouse management software with hundreds of integrations
What are the benefits of WMS software?
Popular WMS Software integrations
Key warehouse management software features
The leading WMS for warehouses, wholesalers and ecommerce
Whether you are B2B or B2C, Mintsoft provides the warehouse management program that helps you to pick, pack and ship your products across the UK and beyond.
Our warehouse management software can be tailored to suit your needs, from simple to more advanced solutions. Whether you operate a single warehouse or multiple stock locations, Mintsoft helps improve your picking management, stock control and replenishment and bulk storage.
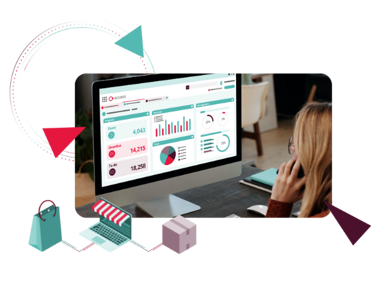
Book a free demo today
Improve warehouse management efficiency with barcoding software
For efficient warehouse management, Mintsoft’s mobile scanning app is available to download on the Google Play store, and can be used on a wide range of supported devices.
- Multi-type Barcode Picking: Multiple types of batch driven barcode picking are available within the app to suit the types of orders in logical location order for maximum efficiency and 100% accuracy.
- Goods-in Processing: Our app makes your goods in process fast, simple and accurate. Book stock easily and receipt and reconcile against pre-existing ASNs or Purchase Orders.
- Transfer Stock: Seamlessly move stock from one location to another - either full pallets or individual units.
- Location Stock Adjustments: Simply scan a location ID to make quick stock adjustments or all SKUS - up or down. The app is incredibly quick at taking control of mixed variant SKUs held in pick bins after a stock take.
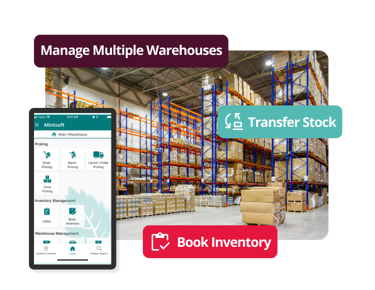
Advanced multi-location warehouse management software
Take control of stock locations and capacity with our cloud-based warehouse management software’s dedicated location management features supporting one or multiple warehouses:
- Multiple Stock Locations: Assign multiple stock locations to individual product lines for pick management, replenishment and bulk storage. Location zone management helps to split and divide picking tasks efficiently across your warehouse workforce.
- Location Labelling: Bulk print location ID barcode labels in any format & size for thermal or laser printers.
- Customisable Location: Types Allocate customised location types to your location IDS to suit your setup such as Pick Bins, Standard Pallets, Double Size Pallets. Location types rules can be set up for storage billing and automatic stock allocation.
- Location Capacity: Instantly view aisle by aisle capacity on an interactive grid and location type capacity from via a dashboard widget.
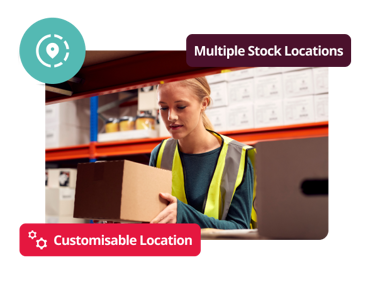
Specialist warehouse tracking software
Designed to be flexible, our warehouse management tracking software can accommodate specialist inventory types - such as perishable goods.
- Best Before Dates: Mintsoft provides automatic FIFO stock allocation management for perishable products with custom expiry date warning notifications.
- Take control of batches and lots: Ensure every piece of inventory that flows through your warehouse can be tracked to its group of origin by tracking which batches have been sent to specific customers in case of product recall events.
- Serial Numbers: Incorporate individual serial number tracking for high value goods on outbound despatch - such as IMEI numbers for high end mobile phones.
- Full Audit Trail: All stock transactions are fully auditable. Every stock transaction is stored with the order ID, customer name and operator that committed the action. These are all easily exportable to excel for reconciling.
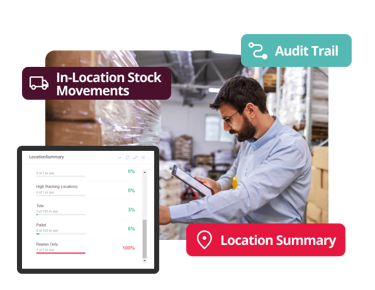
Advanced warehouse management & warehouse inventory tracking
- Tasking/Workflow Management - Control who and how larger, more complex picks are handled
- Pallet & Carton Support - Regulatory compliance with GS2 coding to support picking of pallets and cartons
- Work zones & areas - Further grouping of warehouse locations to include zones & areas
- Quality Control - Quality checking of inbound and outbound goods to ensure stock moving in and out of warehouse meets required standards
- Units of Measure & Volumetric support - Stock capacity management by various units of measure and volume
- Advanced Task Automation - Replenishment, receipt & putaway rules, and picking
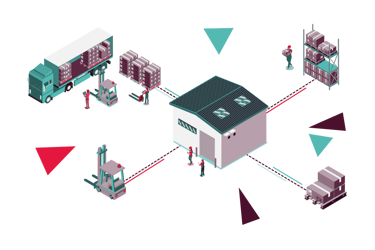
How our warehouse management software helps customers
Efficient warehouse management software for B2B and B2C
A Warehouse Management Software (WMS) is an program that helps warehouse operators and 3PLs manage their warehouse inventory, granting complete visibility and control across the fufillment process. Accessible by smartphone and browser, cloud-based warehouse management & warehouse inventory software helps businesses in the UK and across the globe increase their efficiency by optimising stock control and introducing automated workflows.
Learn about Warehouse Management Systems
Read our complete guide to warehouse management systems to learn about what a WMS is, what one can do, the types and benefits of warehouse management systems, the advantages and disadvantages of a WMS and how to choose the best WMS solution for your business.
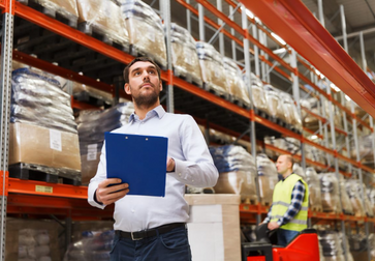
Warehouse management software to help you to pick, pack and ship your way to success.
Warehouse Management Software FAQs
What type of businesses need warehouse management software?
It is important to note that warehouse inventory management softwares are not just for warehouses. With a WMS solution, any company can manage its inventory and distribution processes more effectively - not just 3PL warehouse managers. For example, retailers and wholesalers alike can use a WMS to better manage their stock levels, track inventory movements, and generate reports on product performance. You can be a B2B warehouse operator with multiple warehouses to consider or a B2C ecommerce brand with listings on multiple marketplaces such as eBay, Amazon, and Etsy. Either way, a warehouse inventory management software can help you speed up your business processes as well as reduce errors.
What are the benefits of a warehouse management system?
The benefits of warehouse management software include improved inventory accuracy, improved customer service levels, reduced inventory costs, increased supply chain management visibility, reduced labour, and admin costs, increased speed of service, sales forecasting insight, and more. As a warehouse manager (or a brand that needs to employ one) this will be music to your ears - especially if you are often away, working from the head office.
Is ERP the same as WMS?
A WMS is designed to automate, optimise and improve warehouse operations, whereas Enterprise Resource Planning (ERP) is the automation of processes across all areas of a business, from human resources to procurement.
WMS can be used for both small and large warehouses but comes into its own with floors of over 20,000 square feet and the demands placed upon start to get complex. At this level and above it is sometimes referred to as an ERP system or enterprise resource planning.
How much does the Mintsoft platform cost?
We have 4 tiers of plans, depending on your business size and needs. Our pricing plans also offer custom pricing packages if your requirements exceed the features offered by the maximum tier.
What is the pricing for online retailers?
We have 4 tiers of plans, depending on your business size, and all of our pricing plans for multi-channel retailers can be found here. If your requirements exceed the features offered by the maximum tier, we offer custom pricing packages to suit your business needs as well.
How do you keep track of inventory in a warehouse?
A systematic approach to warehouse inventory management will ensure efficient and reduced costs. This can be achieved through inventory warehouse software, which uses automation and integrations to track inventory movement and stock count in real-time. There are many warehouse stock control methods and best practices you should follow to achieve a seamless operation in your warehouse.
What systems does Mintsoft integrate with?
Access Mintsoft allows you to seamlessly integrate with over 150 sales channels. Marketplace, accountancy, warehouse management software, inventory, shipping and shopping cart integrations are all featured as standard when you use Mintsoft to power your order management processes. Explore our integrations.
What equipment do you need to get started with Mintsoft?
Mintsoft is a cloud-based system, so there are no physical requirements, but we can integrate with the physical kit you have, like your scanners and printers. Getting set up with us is as simple as signing an agreement, and then letting us guide you through the rapid onboarding process.